
If you don’t want to spend money on more powerful measurement tools, use a common ruler instead. A micrometer can be used to measure the thickness of objects, similar to a Vernier Caliper, but with a higher degree of accuracy, often above 0.01mm. Some measures have multi-decimaldecimal ranges and others have measurements with less than 0.1mm. The Micrometer is one of the most common 3D printing tools. In addition to two sets of jaws, this tool resembles a miniature crescent wrench. Vernier calipers are commonly used in the measurement industry to measure. The sculpting tools used in 3D models offer a high level of detail. Copying is a more difficult process, and it is typically accomplished with a 3D Scanner. Standard low-cost measuring devices can be used to obtain a rough estimate of your measurements.
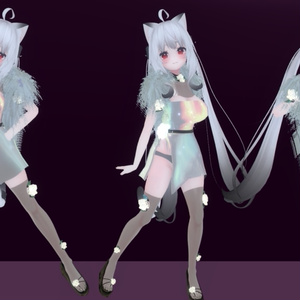
It is far preferable to use digital tools in order to achieve the best accuracy. A dial-accurate meter measures OD, ID, and depth. It is not necessary to get inside to measure depth. If you want to measure anything that fits in its jaws, a dial-cavalier is the way to go. How Do You Measure An Object For A 3d Printer? After you upload your model here, you can place an order for a high-quality 3D print in 18 materials using our online ordering system. Depending on the 3D printer you intend to use, or the software you plan to use for processing the digital mesh, you may receive a different output. To create a 3D model in Maya, it is recommended that you use an. This error correction method is used by me in the same way I used to build the surfaces. Offset surfaces are sometimes incorrectly configured for extremely complex geometry. I usually design my armor pieces in full scale with 1/8 inch wall thickness. Your specific process will require the most recent design specifications. The type of 3D printer you use will have a significant impact on the specifics of how thick and how it will be needed to build your walls. As a result, the thickness of the wall can be adjusted based on the 3D printing technology I’ll be using. Before I can create a 3D model, I first need to create a surface model. It is also critical to consider features such as size, resolution, and file size. In order to create a realistic virtual object, your model must be watertight. Here’s a step-by-step guide to making 3D models in Autodesk Maya. With this information in hand, you’ll be ready to create beautiful 3D prints that look amazing. This article will provide a comprehensive guide on how to size models in Maya for 3D printing, including tips on how to scale your models, how to adjust the units of measure, and how to optimize your model for 3D printing. To get the best results when 3D printing your models, you need to understand how to size them correctly in Maya.
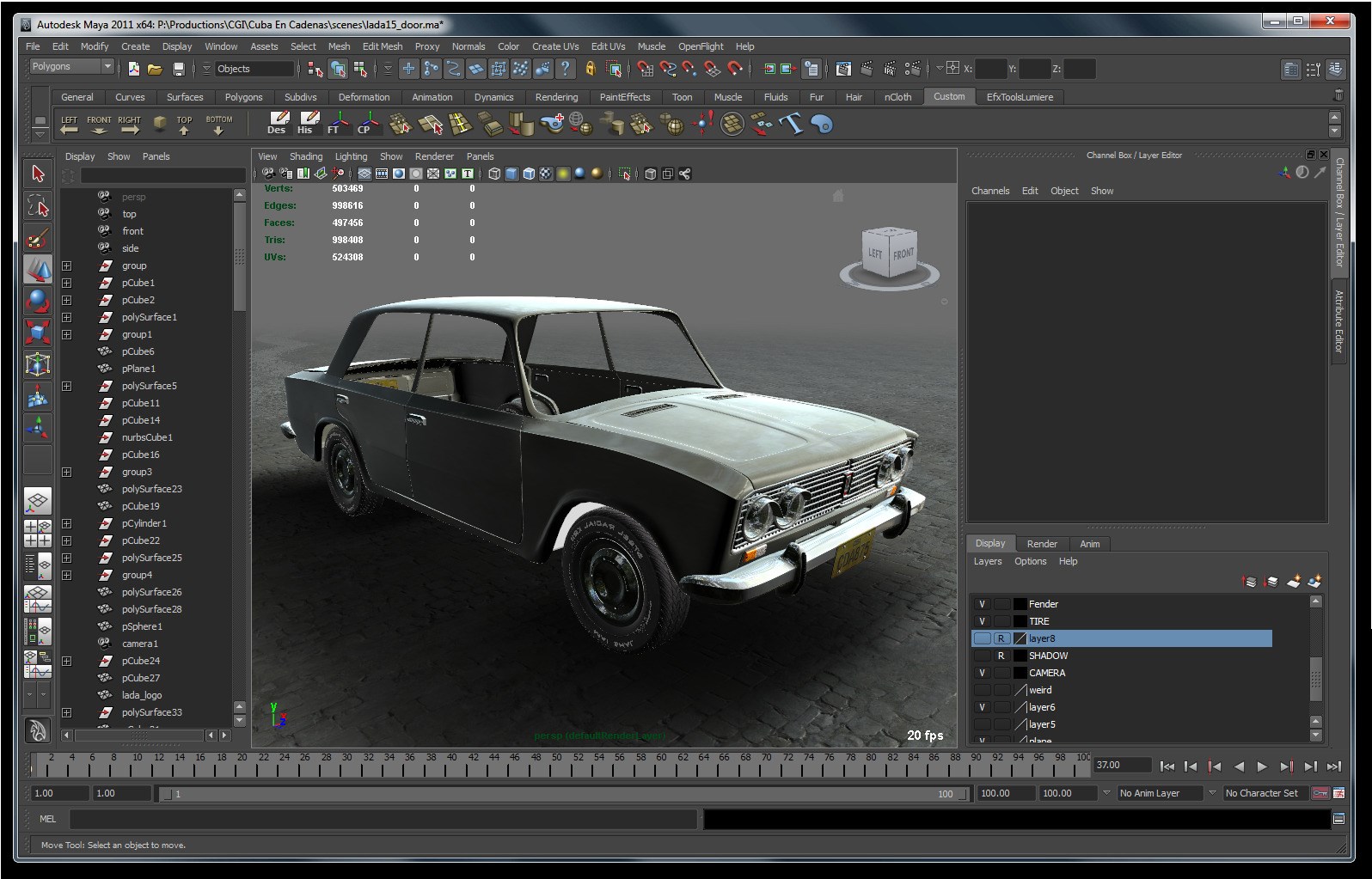
Knowing how to size your models correctly in Maya is an important part of this process. Creating 3D models for 3D printing can be a complex process, but if done correctly, the results can be impressive.
